PROJECTS
WEST METRO ACOUSTICS GROUP
West Metro Acoustics Group, Inc. (WMAG) has an extensive background in acoustic, aerodynamic and vibration diagnostics and sound suppression systems. WMAG was selected to design and build hybrid, reactive silencers for the life support system onboard the NASA Space Shuttle as well as the solid fuel processors for the booster rockets!
Conversely, WMAG expertise was utilized in the development of deep-dive technology (-20 dBA hydro space) for naval vessels, marine salvage and oceanographic exploration. For military and commercial Wind Tunnels, WMAG is repeatedly tasked for analytical design, computer simulation, fabrication and testing of all aeroacoustic systems for low-Mach through hypersonic flows. WMAG has furnished engineering services, design & build systems for all major power generation (EPG) equipment manufacturers requiring maximum noise attenuation. Proprietary computer simulations saved an EPG supplier over $120,000 on a single project! Our analysis and acoustic testing have been the foundation for performing arts’ theater design, worldwide. WMAG was commissioned to provide acoustic & vibration analysis, design and testing services for the new JFK International Air Terminal #4 in New York, including Concord (SST) operations. Following is a summary of the engineering & product support WMAG can offer:
** ACOUSTIC TESTING, AERODYNAMICS / THERMODYNAMICS & VIBRATION
ANALYSIS for IN SITU and/or LABORATORY ENVIRONMENTS **
WMAG maintains strict calibration on a wide variety of aerodynamic analysis, sound measuring, vibration testing and meteorological monitoring instrumentation. These portable systems are utilized in prototype testing, field analysis and in situ certification. Portable, real-time frequency analyzer system can accommodate a microphone spread more than 250 feet and data log complete spectrum/intensities from 0.7 Hz to 22,400 Hz at +/- 0.1dB tolerance every 0.001 seconds. Dedicated computer system supports fast Fourier transforms (FFT) / time correlation for acoustic and vibration measurement and analysis. Forced vibration system provides empirical data on intrinsic impact/vibration isolation capabilities of any building or structure. Aerodynamic tests are accomplished in a computer controlled, open circuit, low-Mach wind tunnel for turbulent or laminar flows. WMAG’s commitment to system analysis extends to the maintenance of a portable Aerodynamic Diagnostics Laboratory, complete with flow visualization capabilities and analytic instrumentation. The Aero Lab is an essential element in product and system testing for compatibility with the clients’ environmental requirements, CFD computer model calibration/verification and long-term system stability and reliability.
** SYSTEM CONSULTATION, PROJECT DEFINITION & MANAGEMENT **
WMAG’s principal forte is the control of environmental, industrial, architectural and blower / fan / HVAC system noise, vibration and aeroacoustics. Our engineers utilize current, state-of-art instrumentation and recorders (ANSI/ISO calibration standards) for problem analysis and solution (compliance) certification. An integral part of our engineering program is the concept of computerized predictive acoustic modeling, computational fluid dynamics (CFD) for volume/mass flow analysis and computer aided design.
WMAG computer models have been repeatedly tested and validated in scores of critical systems including large scale aerospace structures, submarine applications and high reliability telecommunication equipment packages.
These 3-dimensional computer models allow WMAG to analyze hundreds of material array’s and/or subsystems, digitally synthesize their implementation and accurately predict their performance. It should be noted that the WMAG computer aeroacoustic model has the capability to implement infinite sound attenuation for all engine-generator elements not under active analysis.
Further, each of the engine-generator’s component noise sources may be individually analyzed to match specific performance characteristics to the appropriate noise abatement hardware configurations. Existing buildings can be empirically tested for acoustic and vibration containment capabilities and new structures may be computer modeled to assure proposed construction will meet acoustic and vibration criteria.
** SYSTEM DESIGN **
Engineering is supported by a design department consisting of senior designers and draftsmen. Together, our aeroacoustic engineers and design group will generate complete specifications, conceptual illustrations and/or 3-dimensional AutoCAD design drawings to meet the acoustical, physical, thermodynamic and aerodynamic criteria. Due to WMAG’s intimate knowledge of equipment manufacturing, clients can be assured of practical designs which may be economically implemented.
WMAG has earned a positive reputation within the international engine-generator community for dependable, acoustical engineering services in aerodynamics, acoustic diagnostics, system integration (aeroacoustic packaging) and manufactured sound suppression systems for packaged power applications. Engine distributors have entrusted WMAG for silencer retrofits as well as complete enclosure packages, for new and remedial installations, to meet stringent acoustical criteria.
WMAG has long been recognized for its leadership in these fields and so it is with great anticipation that we will look forward to working with you on future projects. Moreover, we would like to assure you that in selecting WMAG, you can do so with great confidence in our ability to deliver what few, if any, other companies can provide.
1. The Architect of the Capitol commissioned WMAG for a power pavilion on rural estate had strict criteria to be unrecognizable and silent.
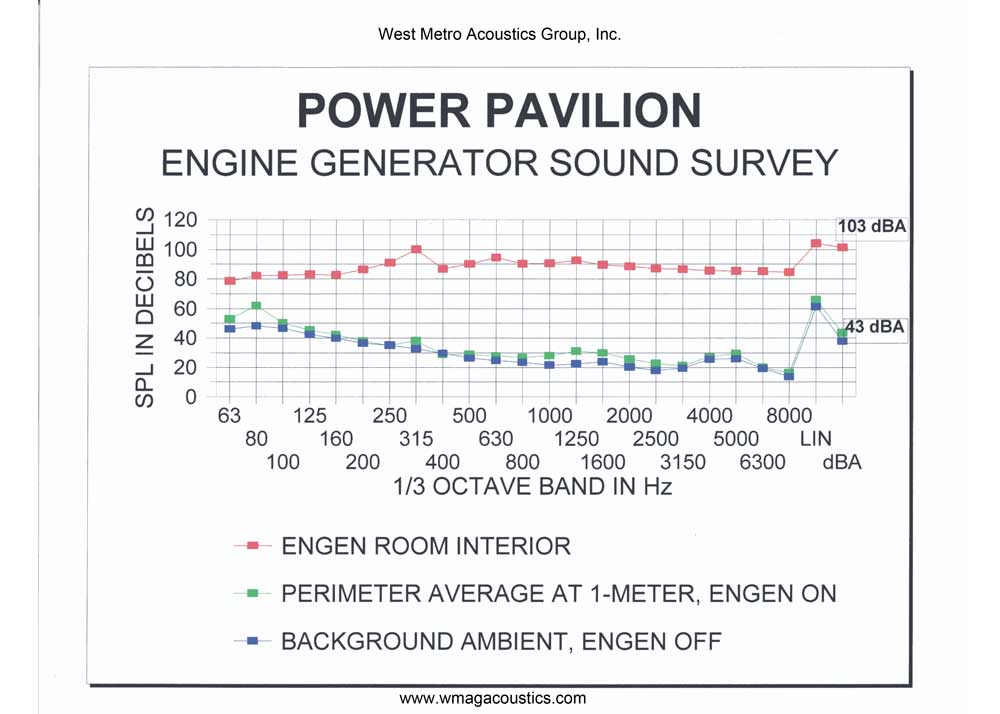
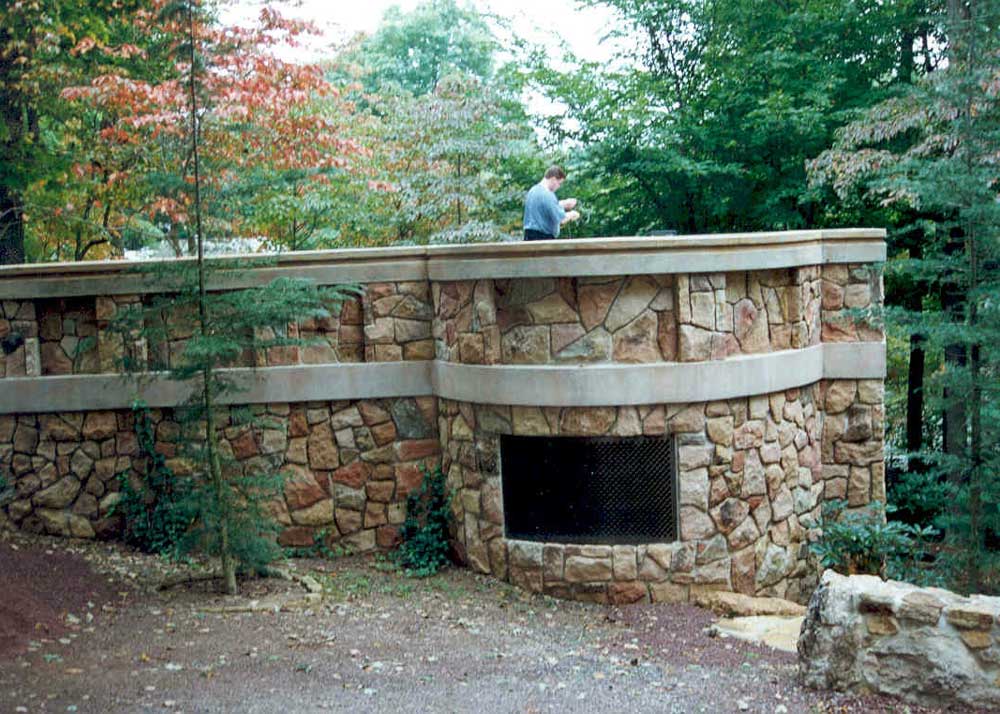
A 300-ekW natural gas GenSet was to be installed within an architectural outbuilding that would blend with the countryside (see photo below) while providing an overt appearance of gentile ambiance. Basic structure was constructed from standard materials with a field stone finish and system integrated by WMAG with all aeroacoustic elements. The following graph (see graph below) reports a 60-dBA average attenuation at 1-meter distance over four (4) walls and roof areas. The red-plot is EnGen room interior, blue-plot is an average at 1-meter from exterior with EnGen off and green-plot is an average at 1-meter from exterior with EnGen on – clearly the rural ambient is louder than the total EnGen acoustic emissions, achieving a 43-dBA at 1-meter (3.2-feet)!
2. WMAG has been tasked numerous of times to reduce residential engine-generator noise in and around the San Francisco Bay area to meet stringent noise ordinances ranging from 40-dBA to 55-dBA at the property lines.
In fact, WMAG is the acoustician of record for the San Francisco Public Utilities Commission as well as the San Francisco Department of Public Works and consults with the Bay Area Quality Control Board on a regular basis to help establish and/or define the noise ordinances for engine-generators! (no photograph)
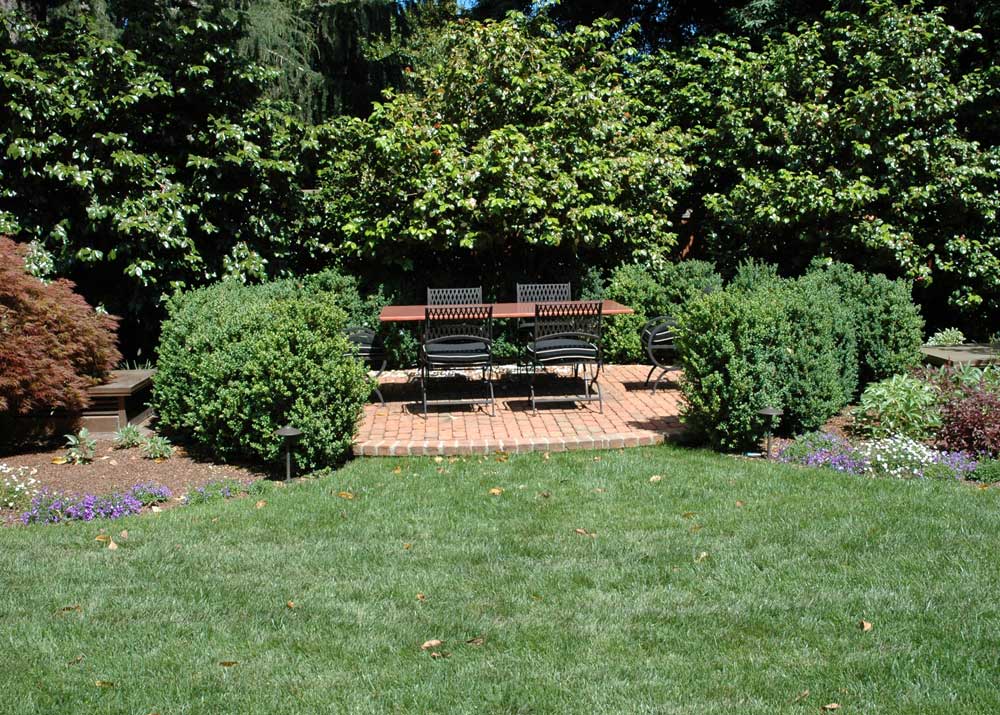
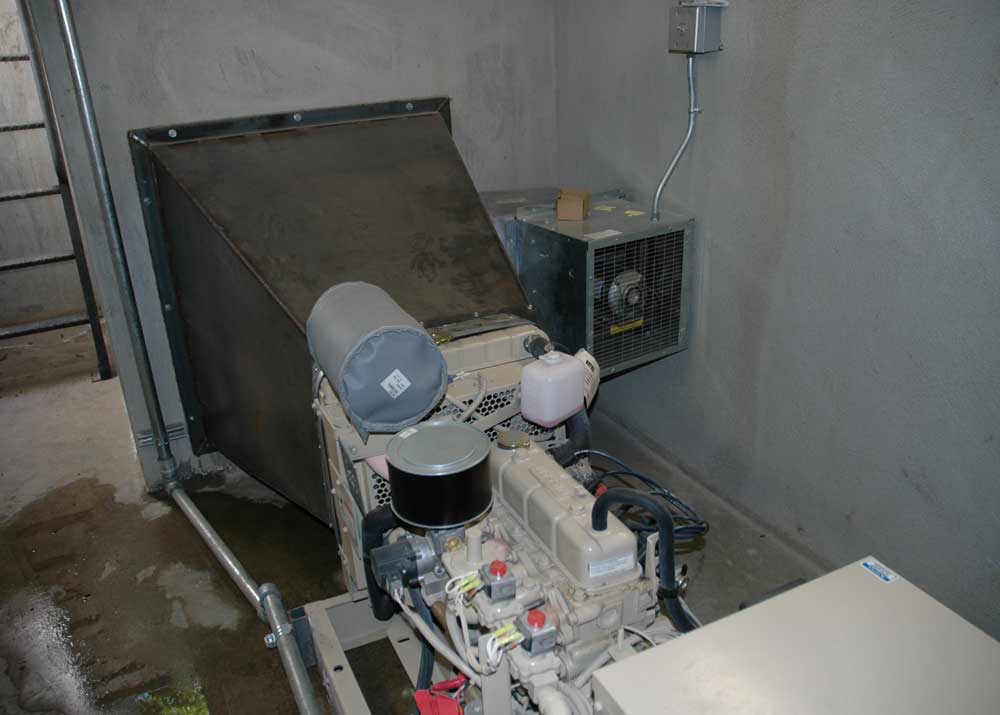
3. A high-end residential home located in Palo Alto, CA required a 25-ekW spark ignited engine-generator to meet 35-dBA at 3-feet! To accomplish this, WMAG buried the GenSet in a concrete bunker, eight feet below grade!
4. A California medical facility required back-up power and WMAG was tasked with aeroacoustically remediating a 25-ekW spark ignited engine-generator housed in an OEM weather-proof, sound attenuated enclosure. 60-dBA at 10 feet was successfully achieved!
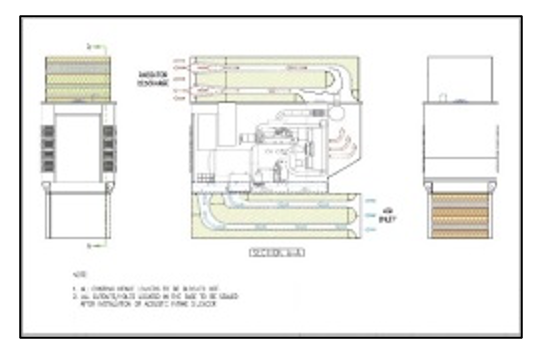
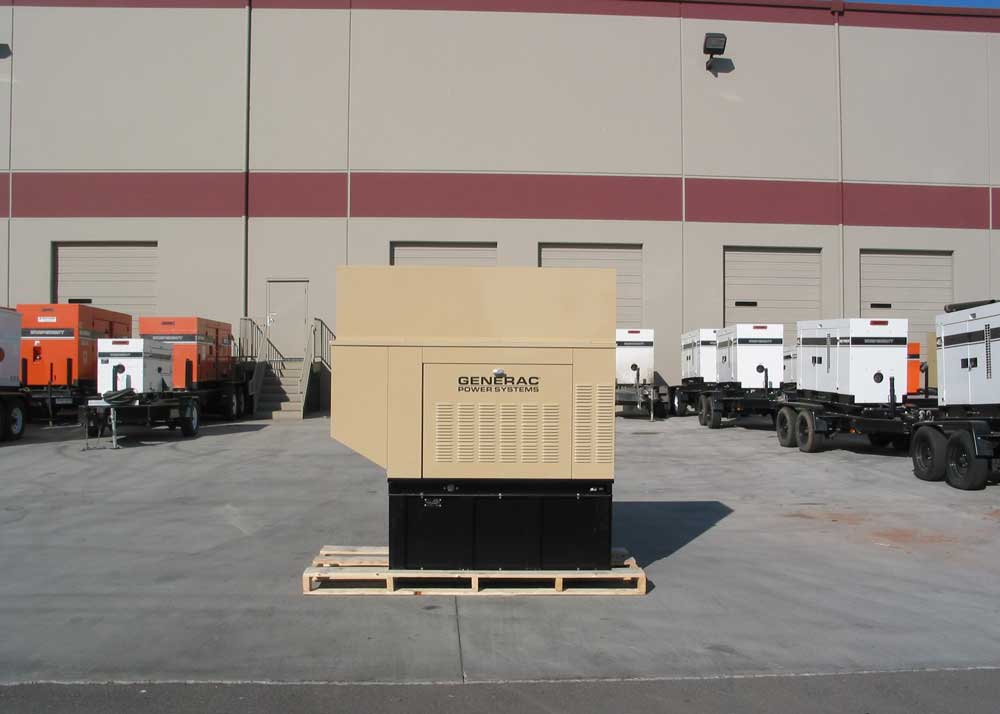
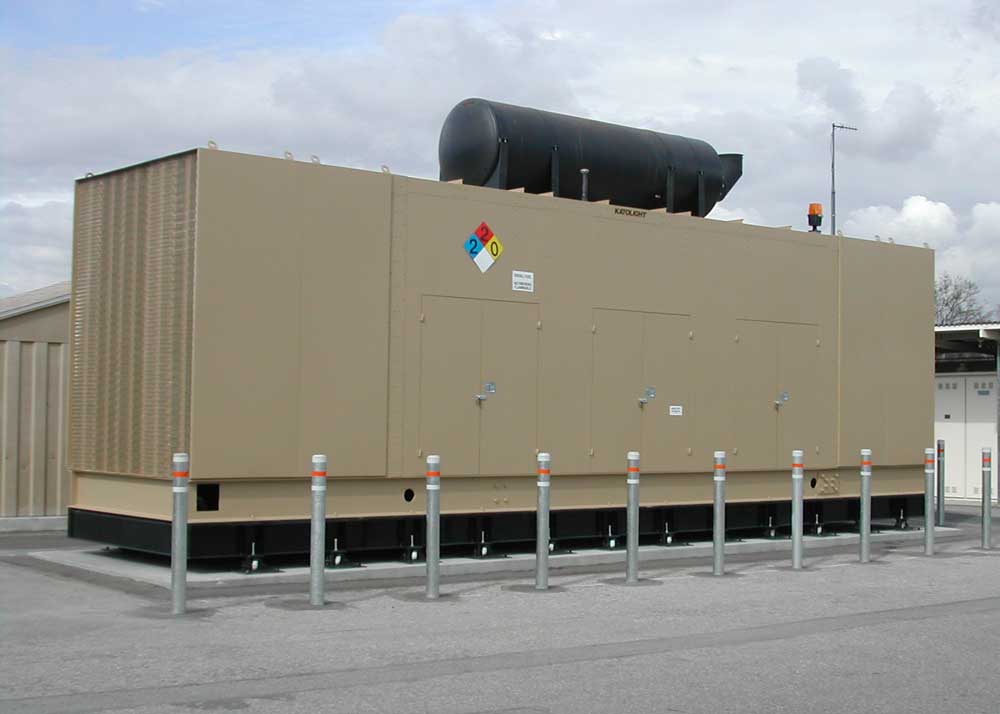
5. A San Jose Water project, WMAG was tasked to aeroacoustically remediate a factory supplied 1600-ekW engine-generator (EnGen) housed in an OEM weather-proof, sound attenuated enclosure.
By removing the factory turn-hoods and utilizing the WMAG air intake and radiator discharge silencing system, a project criterion of 67-dBA at 7-meters (23-ft) was met.
6. A custom enclosure was built to enclose a 2,000-ekW engine-generator set to meet 55-dBA at 15-feet! Incidentally, the engine-generator enclosure was to be located at an elevation of 4,600-feet above sea level, in Grand Junction, Colorado! Aeroacoustics (the combined science of aerodynamics and acoustics) was of the essence!
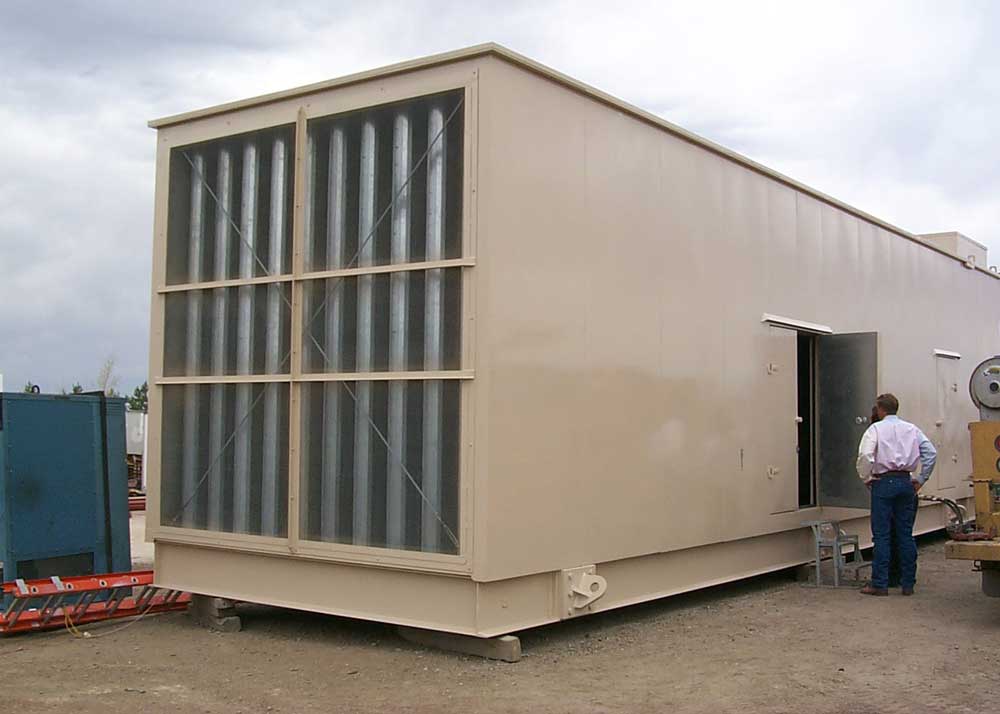
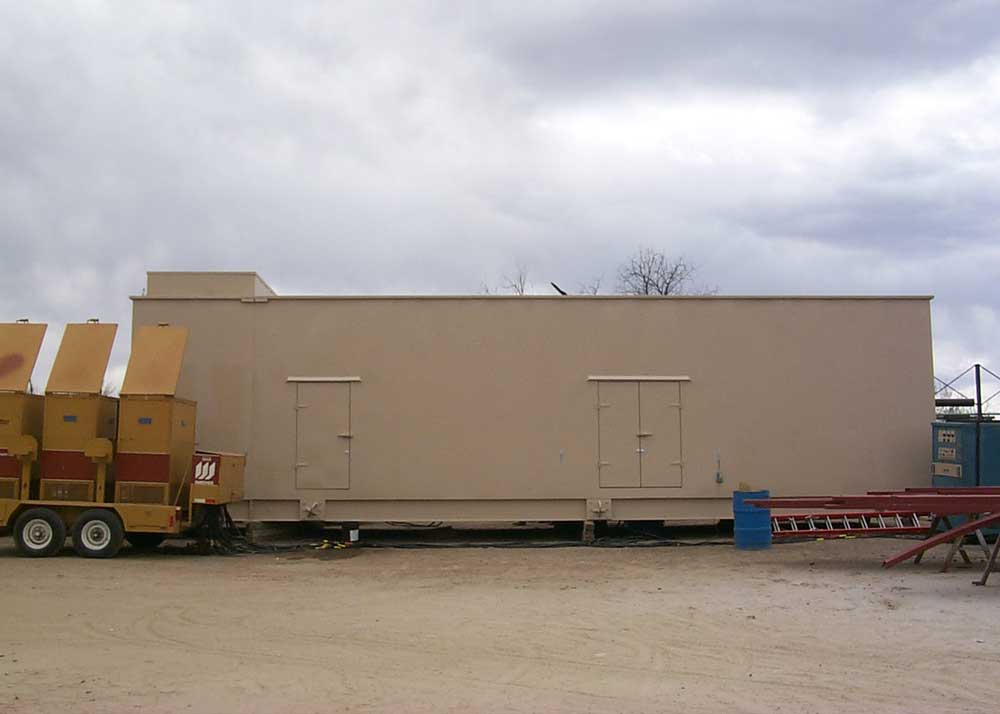
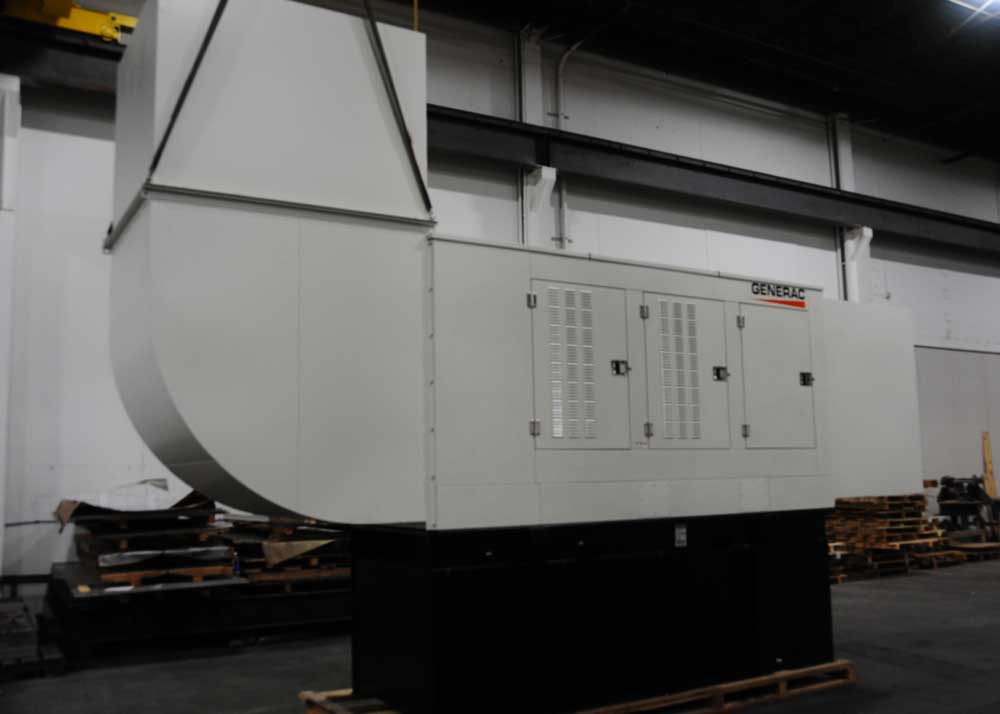
7. WMAG aeroacoustically remediated a Generac SD400 (400-ekW) housed in an OEM acoustic enclosure, to meet a criterion of 73-dBA at 7-meters (23-feet)! WMAG fabricated the air intake silencer, radiator discharge silencer and aeroacoustic turn-hood
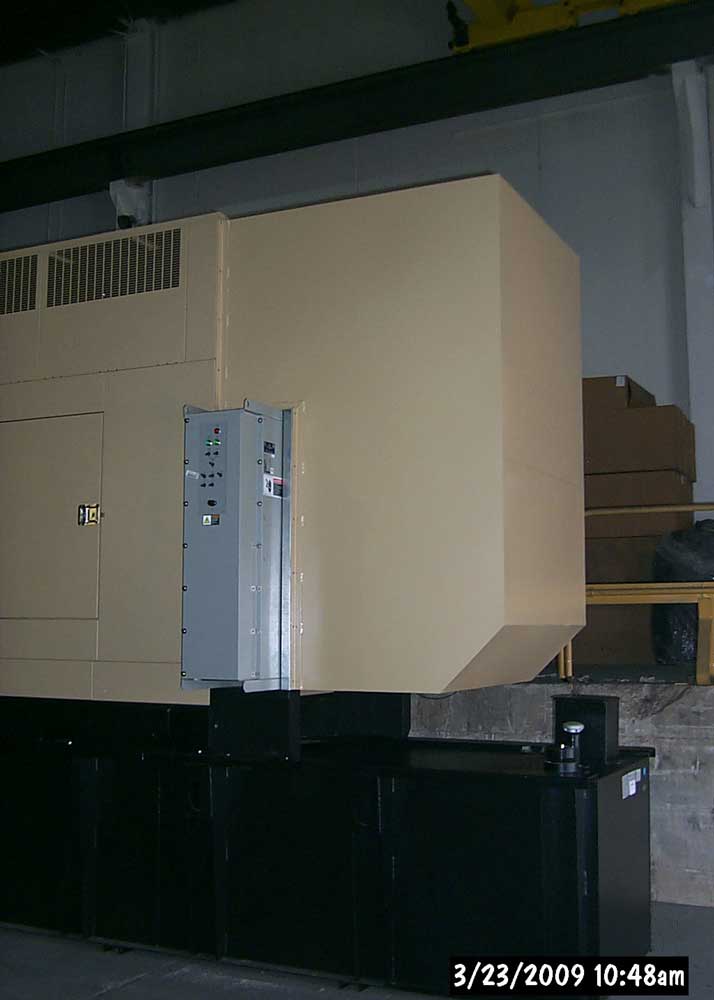
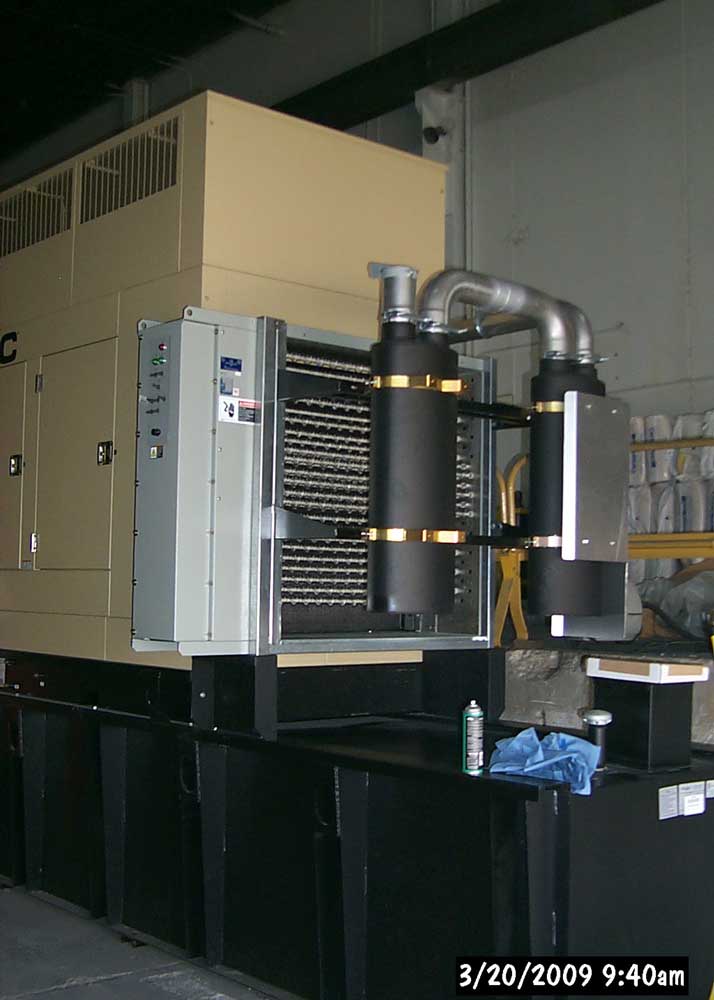
8. Located in West Long Branch, New Jersey, WMAG fabricated the turn-hood to accommodate an Avtron model #K711 (115-kW) radiator-mounted load bank. This application required aerodynamic flow conditioning.
9. The San Juan WTP project picture depicts a 500-ekW EnGen with a Loadtec 250-ekW radiator-mounted load bank built within the radiator discharge silencer. The acoustical criterion for this application was 85-dBA at 7-meters (23-feet), required aerodynamic velocity pressure distribution and airflow normalization
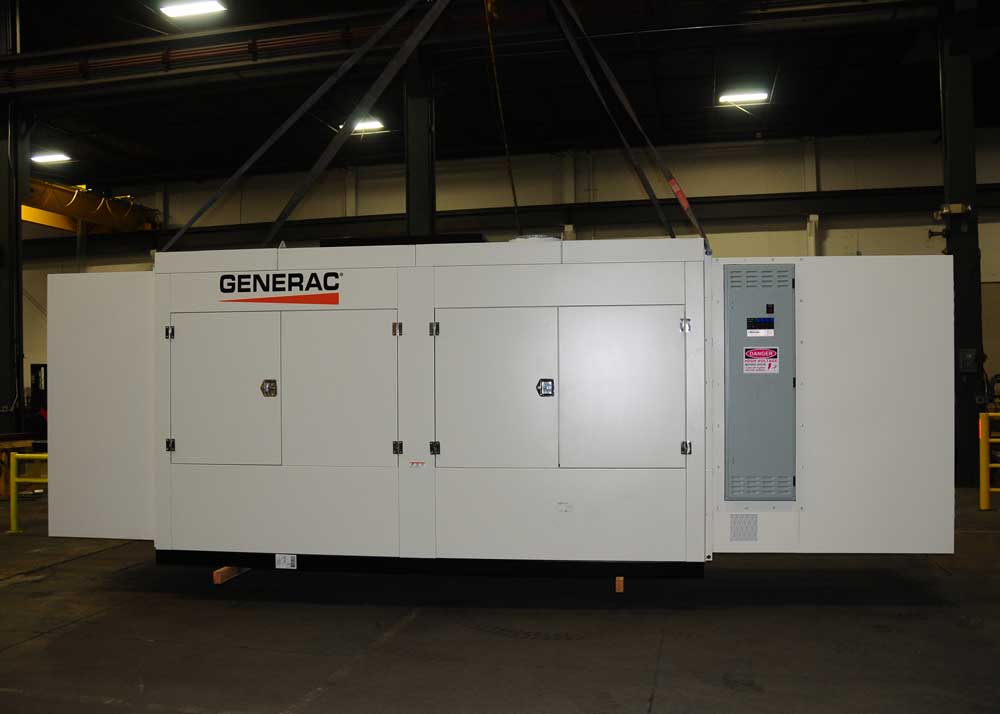
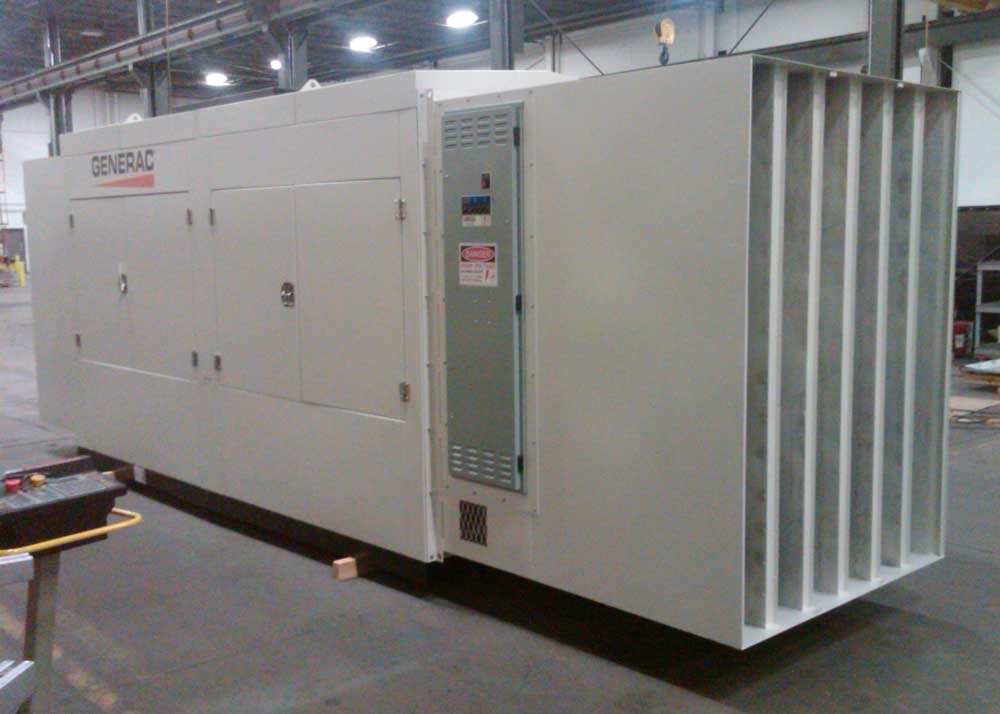
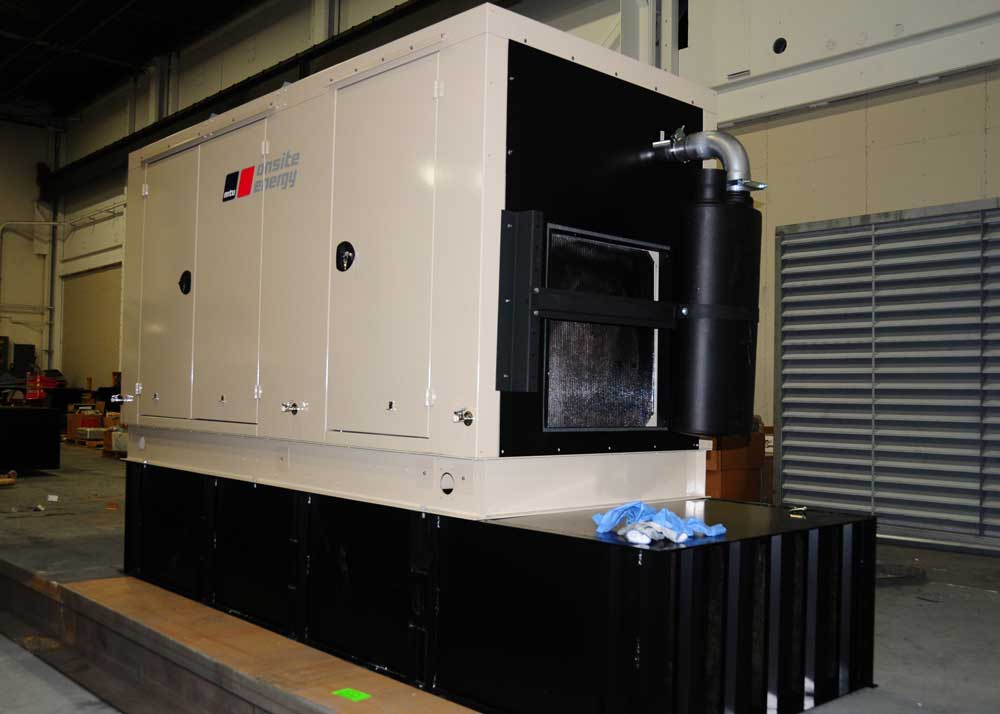
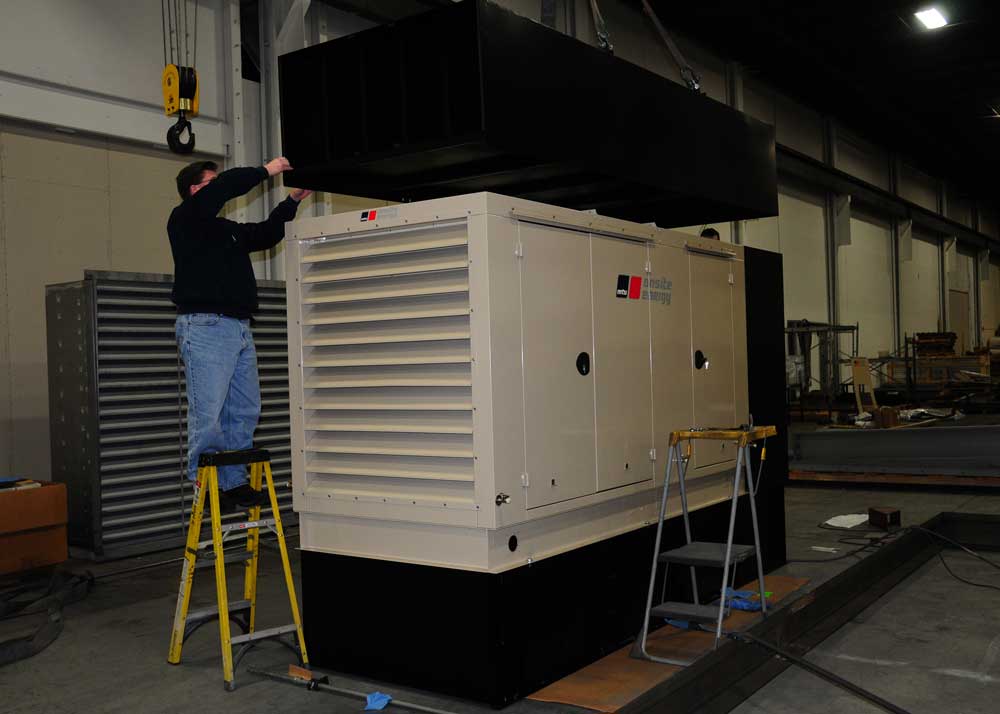
10. For an MTU distributor located in Denver, Colorado, WMAG modified a weather-proof OEM enclosure utilizing an “Over & Under” configuration. The pictures depict a 125-GC6NLT1 (125-ekW) spark-ignited engine-generator in the final stages of assembly. The degree of silencing achieved was 58-dBA at 20-feet!
11. 41-story (449-foot) residential / mixed use tower project located in Midtown Manhattan, NY (Turtle Bay/United Nations area) required a custom enclosure for a 750-ekW diesel-fueled engine-generator set with a mandatory acoustical criterion of 65-dBA at 1.5-meters (5-feet). To lift the enclosure up to the rooftop, located on the 41st floor, the enclosure was built in 3-sections to accommodate the crane’s maximum 21,000-pound lifting capacity.
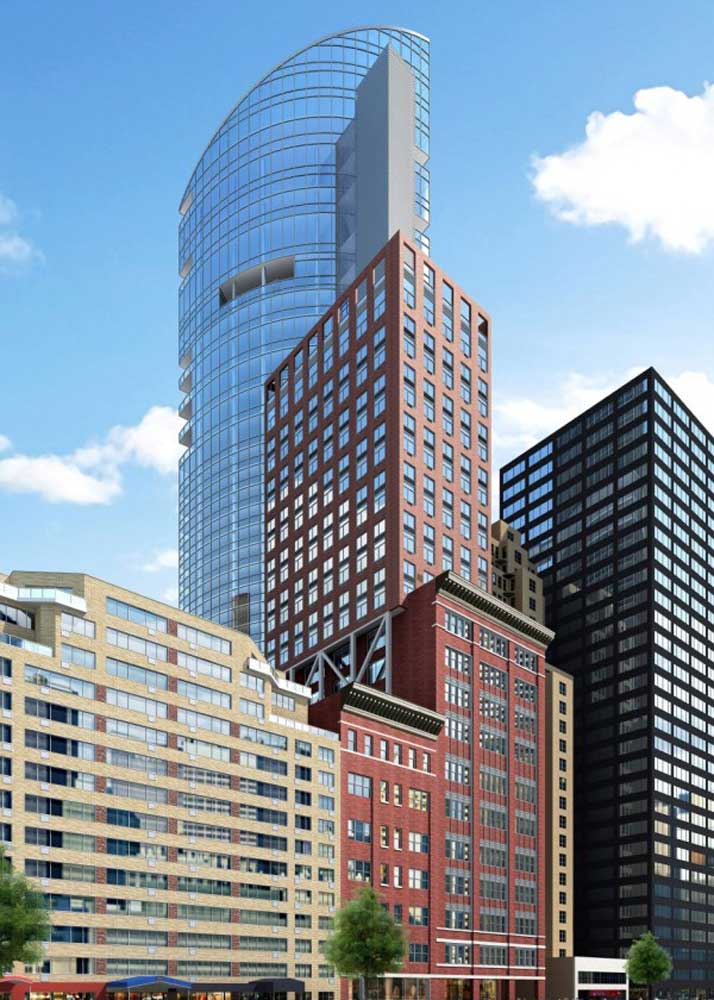
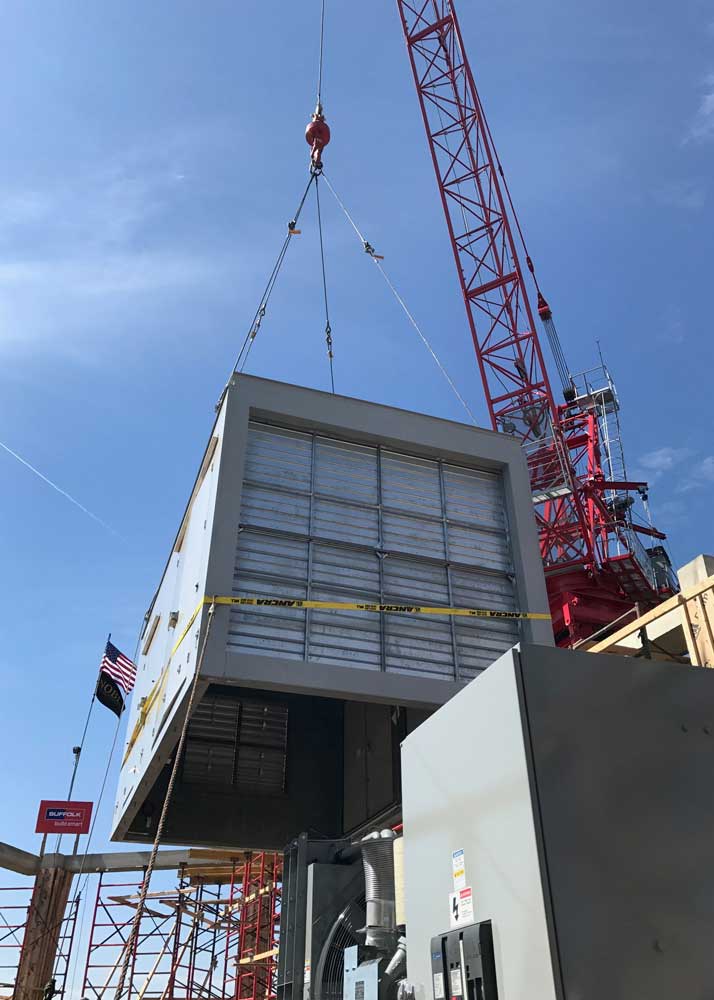
12. WMAG collaborated on a design-build project for the Broad Creek WTP (Water Treatment Plant) located in Fort Washington, Maryland, near the Washington DC Memorials.
A cumulative total of 4.5-megawatt (2 x 2,250-ekW) engine-generator sets were enclosed within an architectural structure and sound attenuated with air intake and radiator discharge silencers, a primary and secondary engine exhaust-gas manifold silencers and interior absorption panels. Project criterion called for 45-dBA at 9-meters (30-feet) with both EnGen’s running simultaneously!
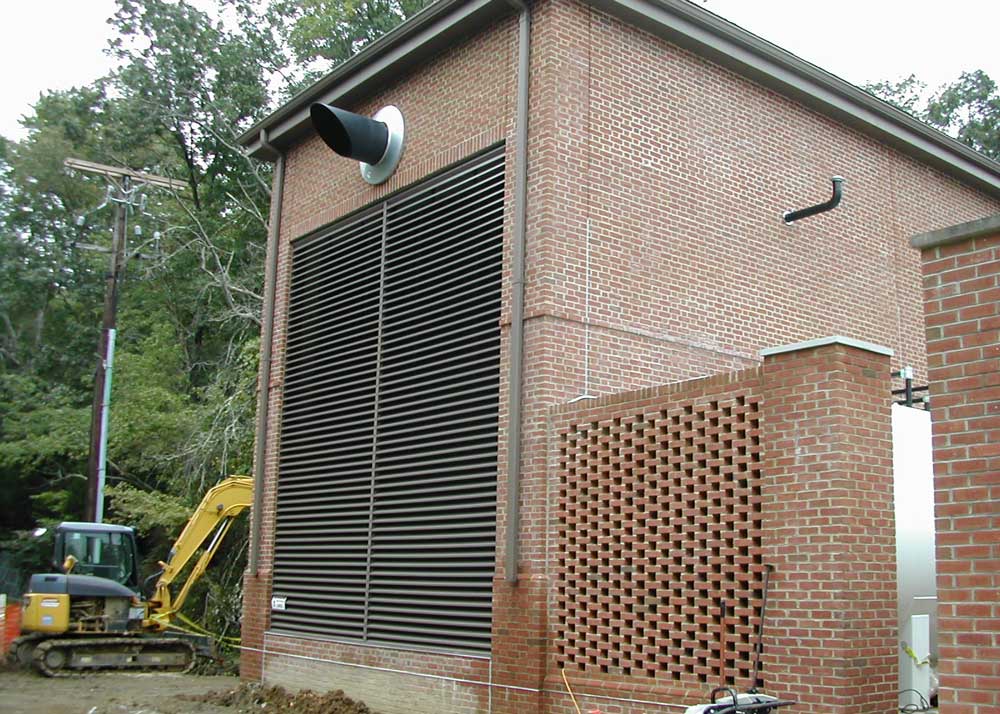
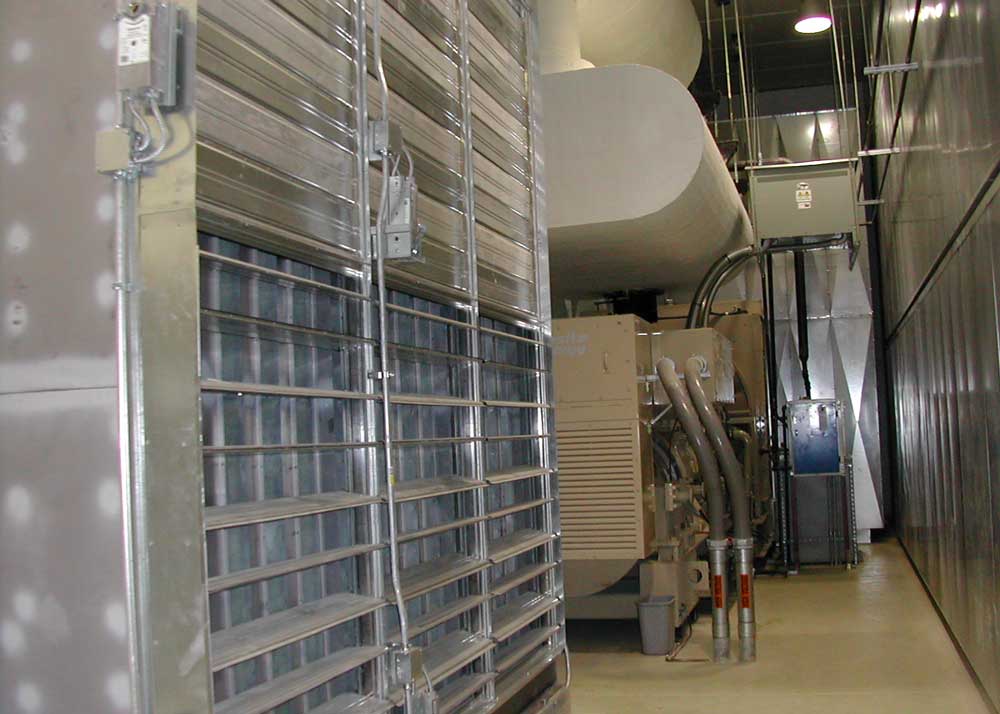
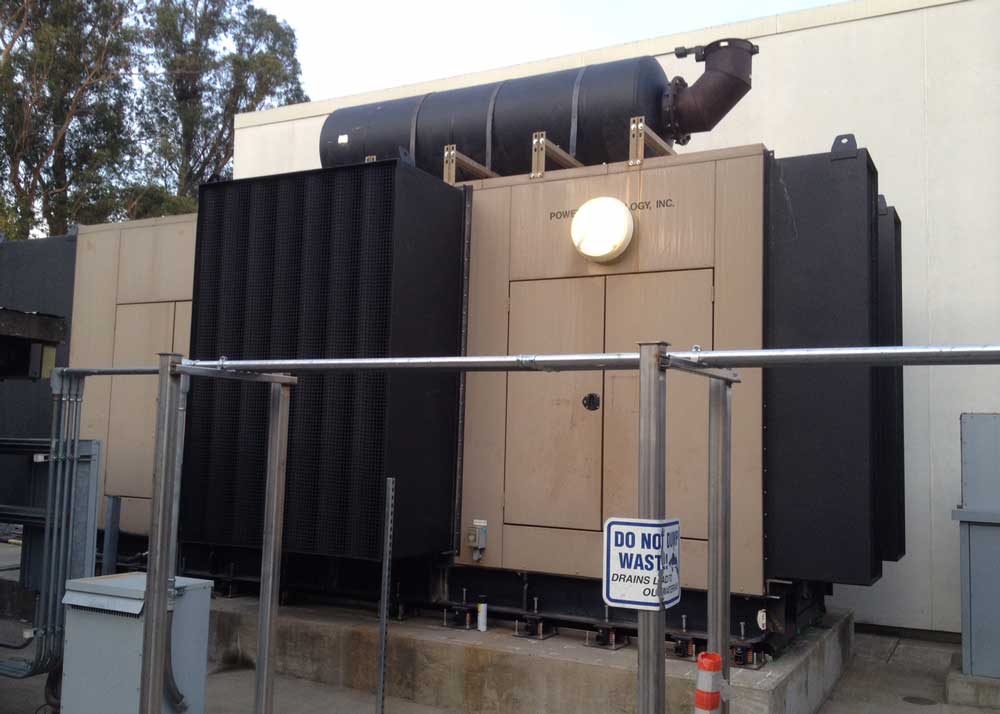
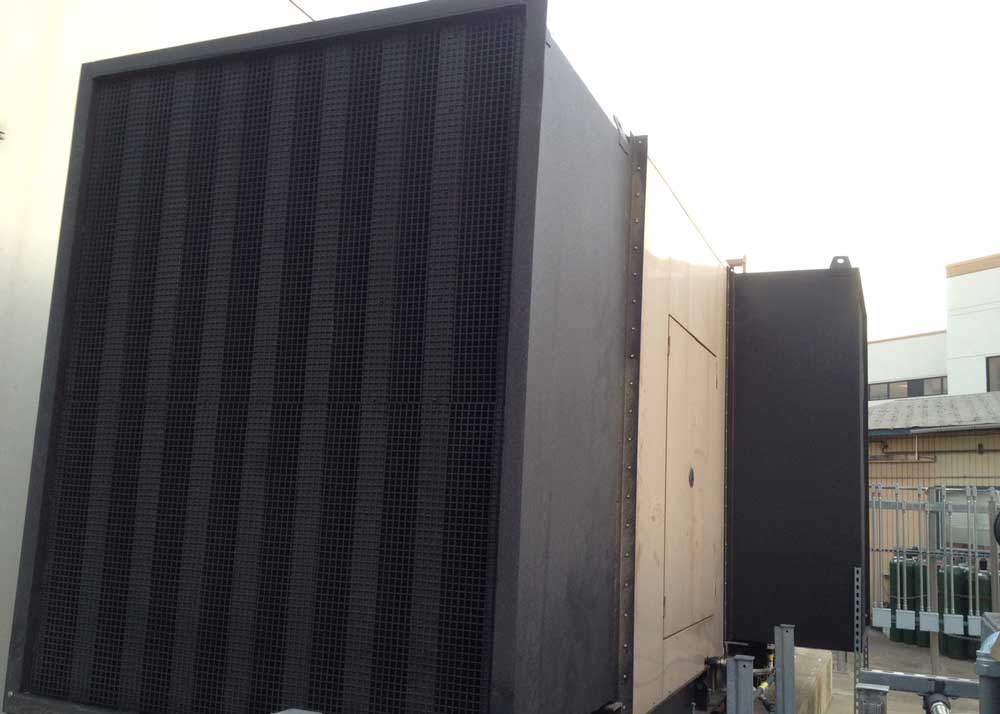
13. The administrator for the Santa Rosa Memorial Hospital had been receiving noise complaints resulting from their 1500-ekW emergency stand-by EnGen.
WMAG was tasked with onsite retrofitting the existing OEM enclosure utilizing bolt-on air intake & radiator discharge silencers. In addition, the WMAG aluminum-built silencers had to comply with California’s Office of Statewide Health Planning & Development (OSHPD) regulations and seismic requirements. The acoustical design goal was a 20-dBA Noise reduction at 23-feet.
14. The Blake School, located in Minneapolis, MN, installed a 400-ton, air cooled, rotary compressor to service their new expansion.
A location had been chosen to minimize noise impact on residential neighbors (NAC-1 land use) and the school itself. However, intrinsic site topography aggravated chiller noise emissions, which exceeded the local noise ordinance, resulting in legal action. WMAG provided the system design, acoustic hardware fabrication, installation supervision and performance warrantee for acoustics and chiller operating parameters. System acoustic performance (dynamic insertion loss or noise reduction) was tested at a nominal 40-dBA at 1-meter (3.3-feet) distance.
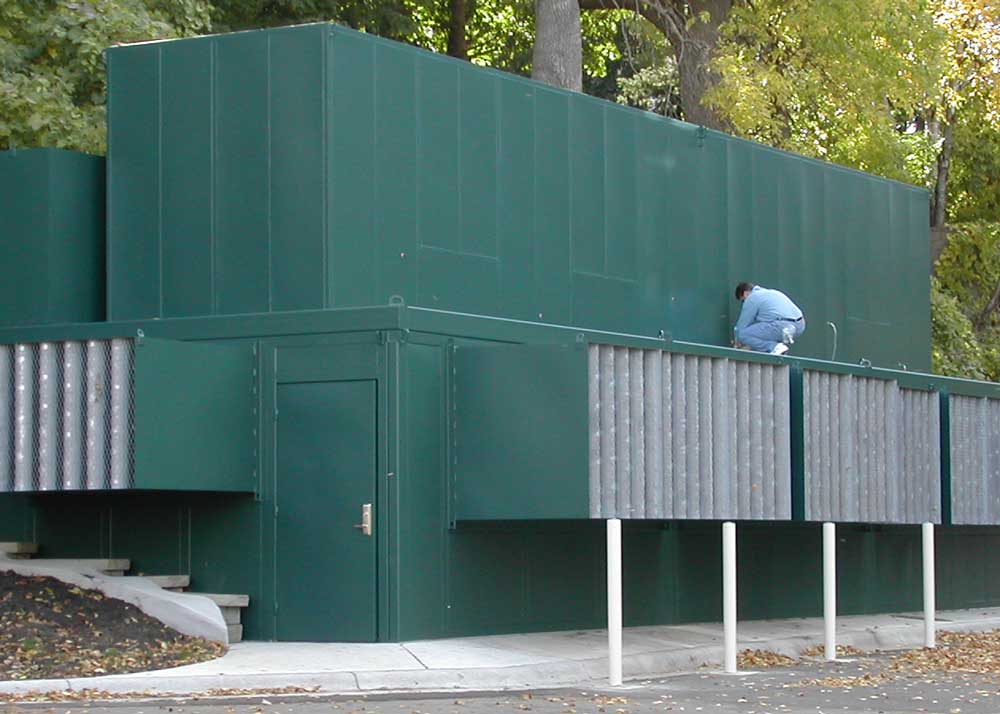
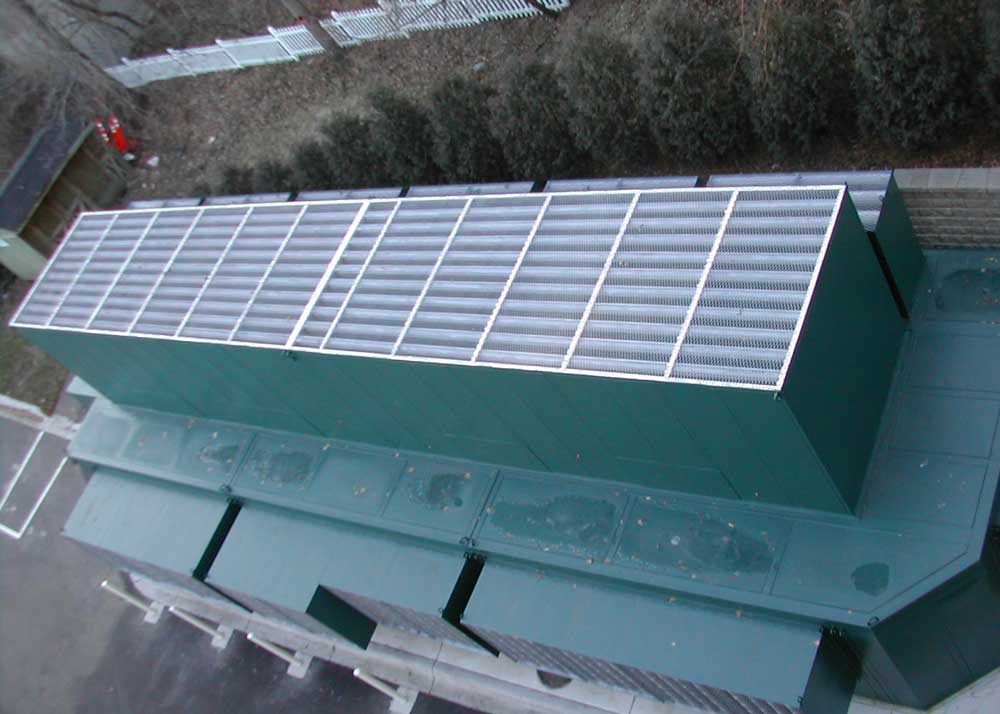
15. Located in Minneapolis, Minnesota, La Rive Condominiums is a 27-story luxury tower located on the banks of the Mississippi river.
To bring their 440-ton cooling tower into compliance, WMAG designed, fabricated and installed a stealthy noise control system that demonstrated a noise reduction from 114-dBA (no WMAG silencing) to 47.9-dBA (with WMAG silencing) a dynamic insertion loss of over 66-dBA at 1.5-meters (5-feet) distance, while providing lower operating costs due to improved aerodynamics!
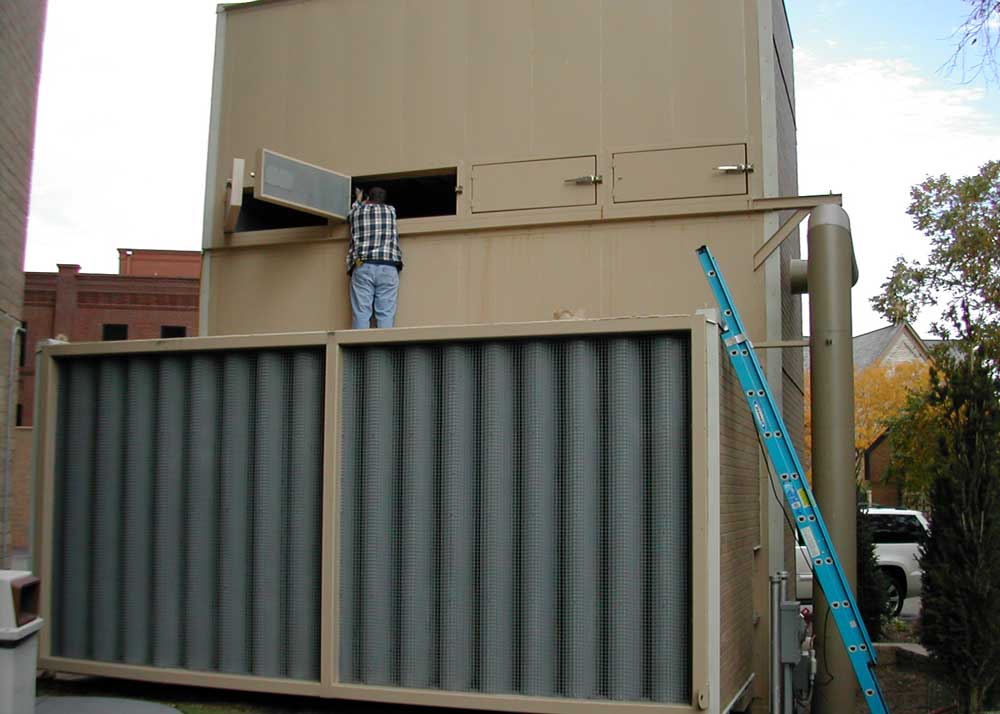
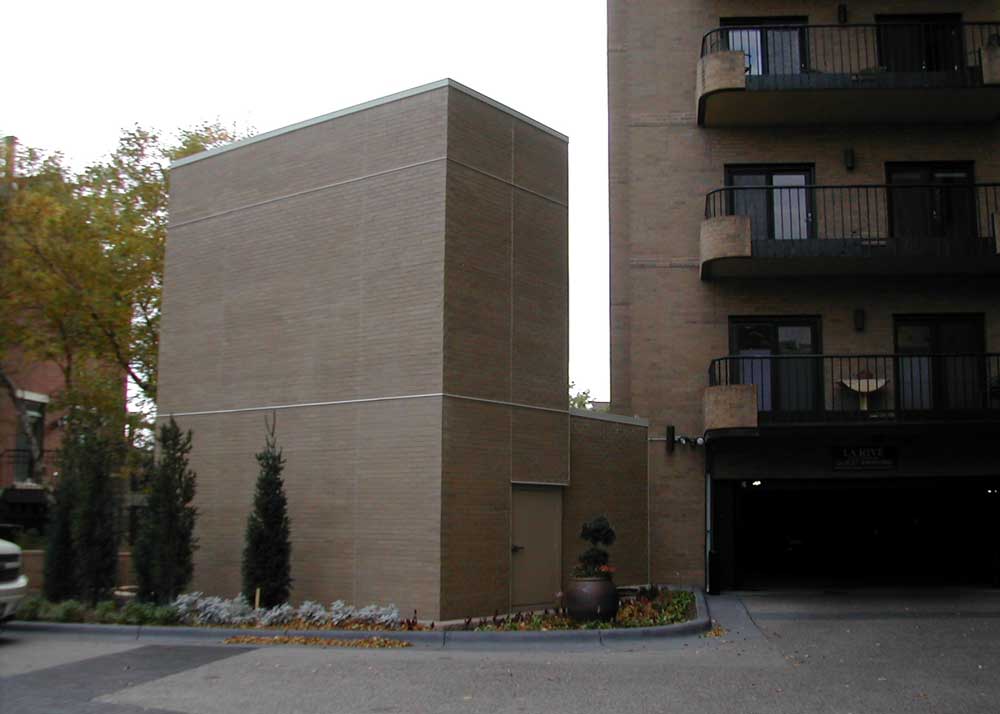
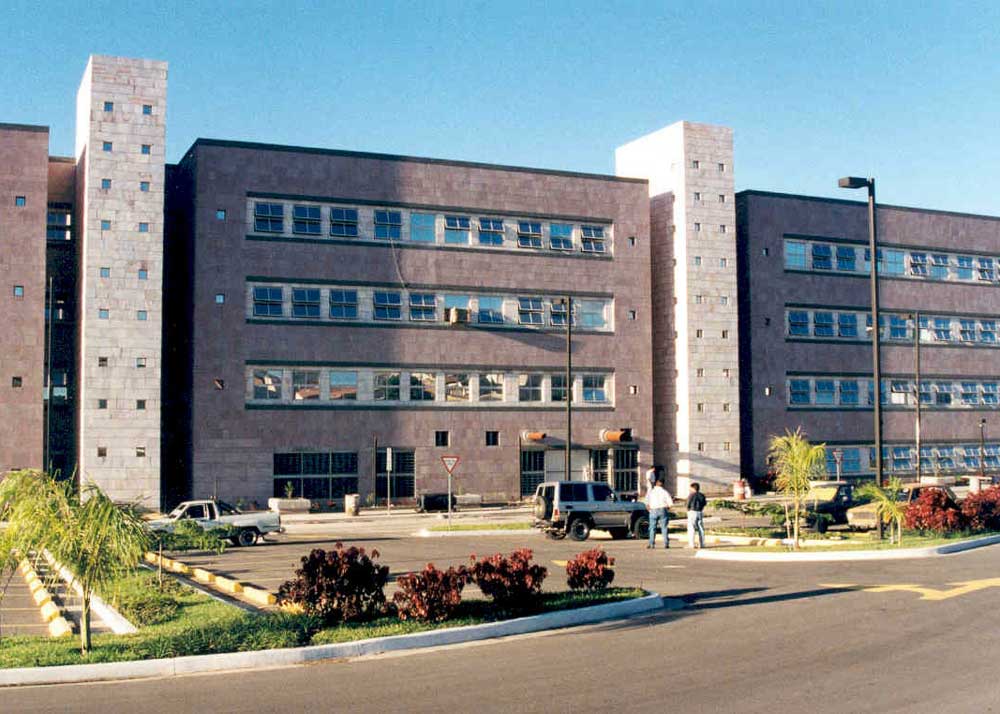
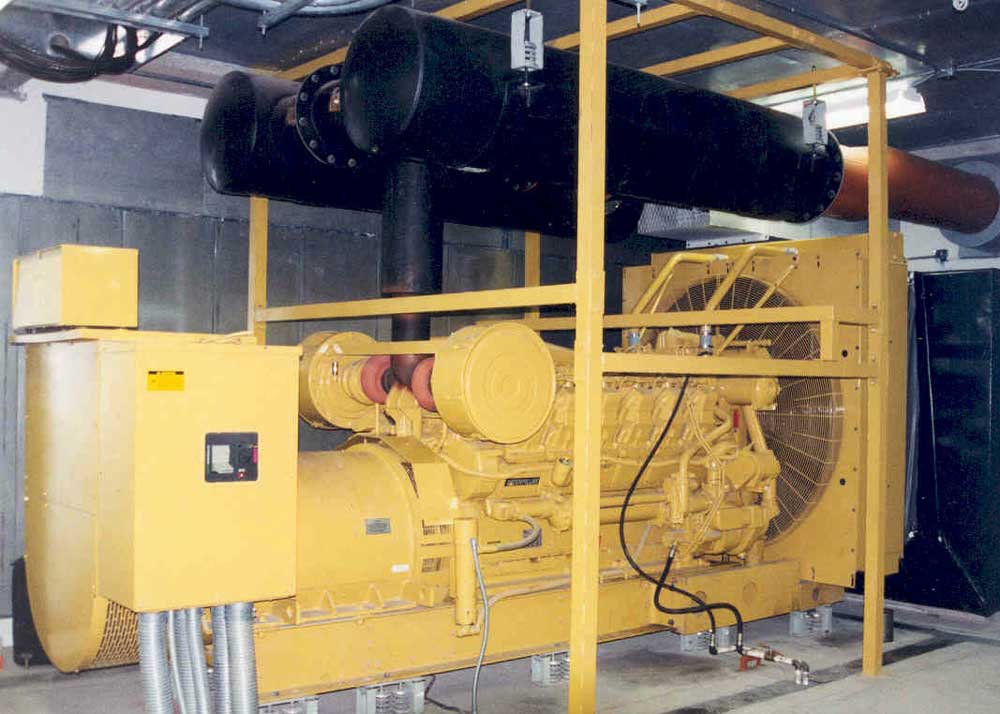
16. Located in Tegucigalpa, Honduras, Central America, The Banco Centroamericano de Integración Económica (BCIE) consulted with WMAG to analyze, system design and fabricate the acoustic hardware to sound attenuate the engine-generator room.
The GenSet room, consisting of a 300-ekW and 1,500-ekW, was directly below the computer programmer’s library! Aside from the aerodynamics and acoustics, the noise induced vibrations from the engine-generators, could not be allowed to transmit through the buildings structure. The acoustical design goal was a 20-dBA Noise reduction at 23-feet.
17. WMAG was commissioned by British Petroleum (BP) Americas to design, fabricate, supply and supervise installation of an acoustic enclosure for a well-head compression system located in the high desert [over 2,134-meters (7,000-feet) above mean sea level] of Southwestern United States of America.
Further, the enclosure was to be passively ventilated (no auxiliary fan) and meet the COGA criteria of 65-dBC at 22-meters (75-feet)! Not only was a dBC weighted criteria an unprecedented issue but the site’s elevation above sea level and extreme ambient temperature made hardware design an aerodynamic challenge! WMAG met the challenge, aeroacoustic criteria and schedule!
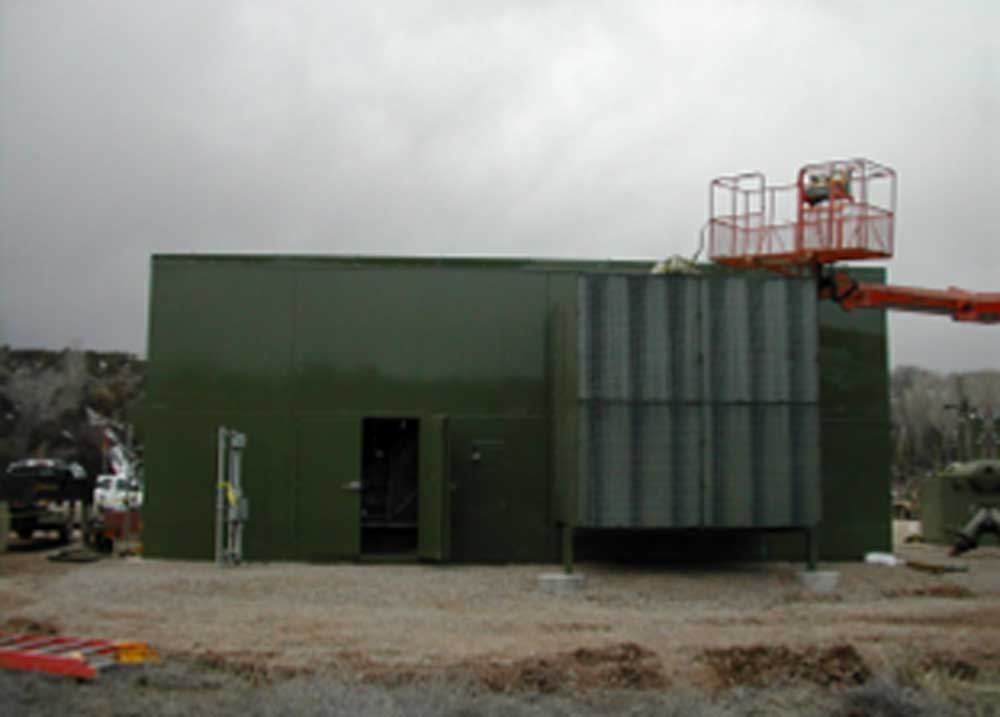
18. Data Center located in a residential area near Denver, Colorado [1,658-meters (5,440-feet), elevation ASL] had a third-party sound test two (2) individually enclosed 2000-ekW EnGen’s and were measured at just under 80-dBA at 7-meters (23-feet) distance, exceeding the contractual criteria of 60-dBA at 7-meters (23-feet)! The enclosure fabricator (Packager) commissioned WMAG to develop a fix to be accomplished on site.
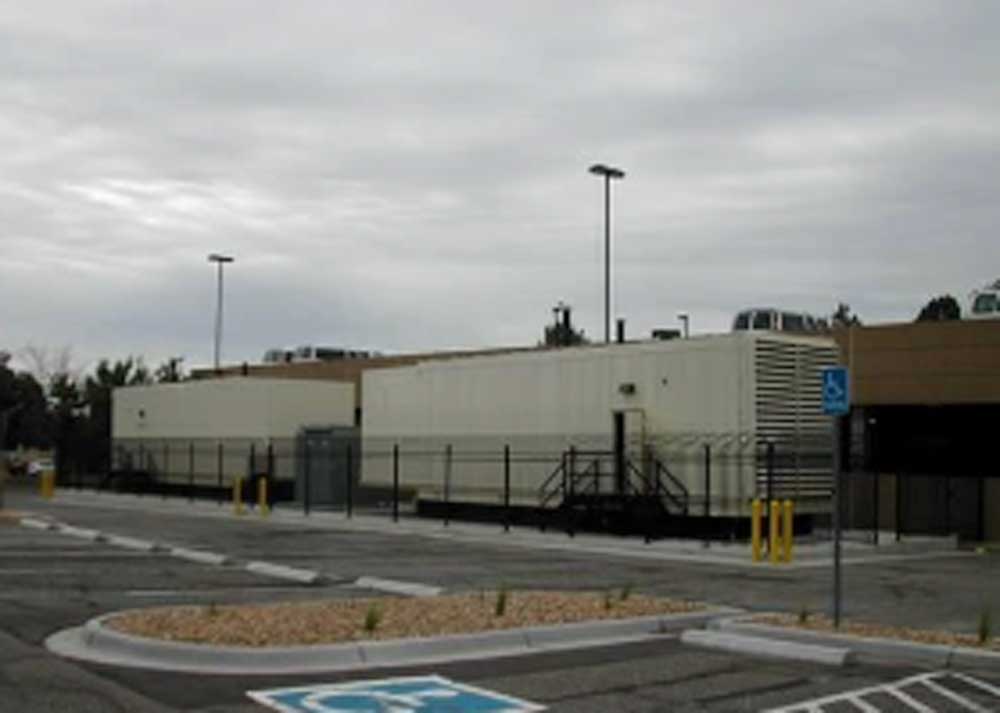
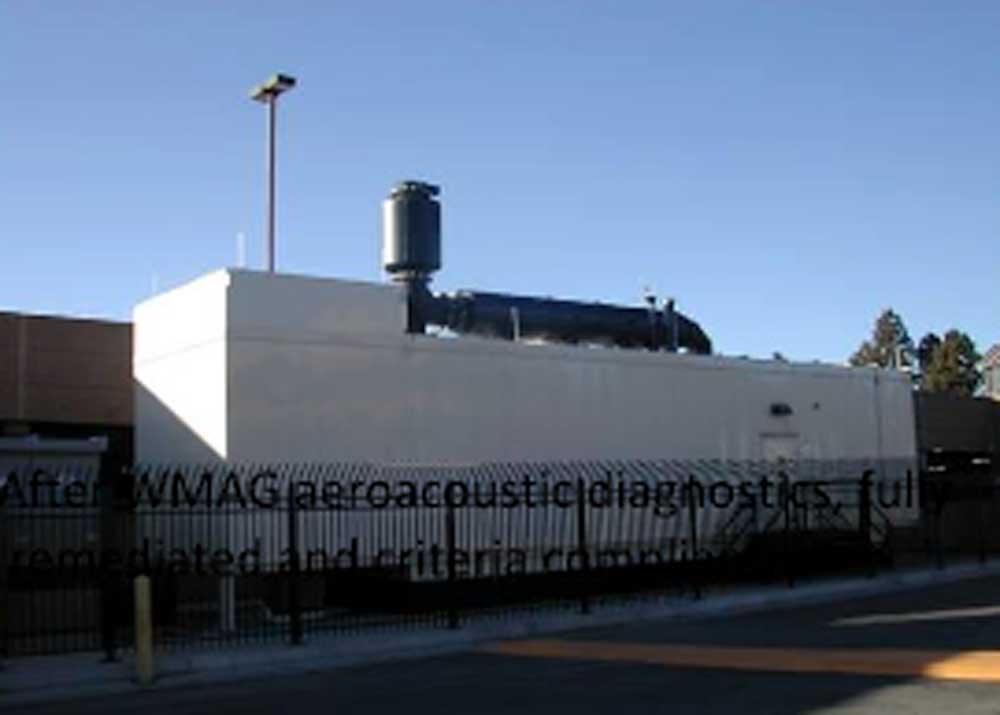
WMAG designed an aeroacoustic 3-D computer model using the Packager’s as-built drawings, equipment bid specifications and manufacturer’s EnGen parameters. Computer modeling confirmed that the enclosure’s radiator discharge (Raddis), Intake, enclosure wall construction and engine manifold exhaust mufflers were, indeed, all out of compliance! Further, the aerodynamic computer analysis (CFD) suggested the enclosure’s added static pressure exceeded specified limits (160% over) and was subject to a high temperature EnGen shut down during extended run time and heavy electrical loads!
The Packager authorized WMAG to visit the EnGen site and accomplish aeroacoustic testing, including dynamic airflow visualization. Empirical test results validated all computer modeling predictions and added an observed engine exhaust gas recirculation issue to the list of the enclosure’s liabilities!
WMAG utilized computer aeroacoustic modeling to design a secondary exhaust muffler and tuned stack resonator to bring the exhaust system into compliance, without exceeding backpressure limits, and eliminating recirculation. A cost effective, airflow conditioning, drop-on silencer module was designed for the vertical Raddis stack. The Intake section was site modified with WMAG airfoil baffles using static regain technology to greatly reduce aerodynamic losses. The completed remediation was third-party tested to be 58-dBA at 7-meters (23-feet), below the contractual limit! Remediated system aerodynamics brought the enclosure’s total static pressure loss down to 12.78-mmH2O (0.503-IWG), well within the EnGen manufacturer’s allotted tolerance for site elevation.
We are always ready
to help you
West Metro Acoustics Group, Inc.
2909 Edgewood Avenue North
Crystal, Minnesota 55427-3016
United States of America
(763) 544-3129 | Mark’s Direct
(612) 220-7028 | Scott’s Mobile